There are risks associated with keeping inventory offshore, but bringing it home is not a decision to make lightly.
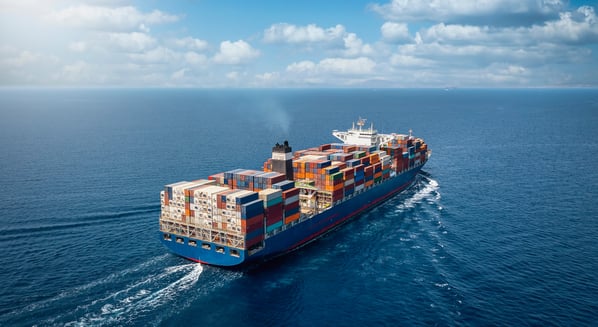
Keeping inventory offshore exposes your business to various risks that can disrupt your supply chain, including geopolitical instability, natural disasters, transportation slow downs, and even port closures – all of which can result in significant delays in getting products to customers.
When inventory is held overseas, it can also be harder to manage quality control, which can lead to customer complaints and product recalls.
In addition, longer delivery times and currency fluctuations can increase inventory carry costs, tie up working capital, and reduce your profit margins. And intellectual property risks, such as counterfeiting, piracy, and theft, can result in lost revenue, legal fees, and damage to your company's reputation.
So why isn't everyone rushing to bring their inventory back home?
What does it mean to reshore your inventory?
"Reshoring" or "onshoring" means bringing inventory or production back to a domestic market from an overseas location; it can involve establishing new production facilities in your home market, changing your supply chain partners, and even changing your product design so you can produce goods domestically instead of offshore.
For most companies, a decision to reshore inventory will have many downstream ramifications and should not be made lightly. Yet there are good reasons to give it serious thought.
Reshoring can reduce your company's dependence on offshore suppliers, for example, which can minimize supply chain disruptions and significantly reduce transportation costs. And moving operations closer to home can make it easier to maintain consistent production standards. Investing in domestic manufacturing can also create new jobs that can lead to positive economic benefits for local communities.
Aviation companies face unique inventory challenges
Over the past few years, there has been a growing trend among aviation companies to move their supply chains closer to their manufacturing and assembly plants.
By reshoring inventory, they can minimize costs and ensure that parts and products meet consistent production standards and regulatory requirements. This level of control is essential in an industry where safety and reliability are paramount. Other aviation supply chain problems to be avoided include:
- Parts shortages - A shortage of complex and highly specialized aviation parts can result in delays, grounded aircraft, and lost revenue.
- Product recalls - Quality control is crucial in aviation; even minor defects can have catastrophic consequences. Parts that are not manufactured or inspected to the highest standards may need to be scrapped or recalled, resulting in additional costs and delays.
- Regulatory compliance - Aviation parts companies must comply with a wide range of government standards, such as the Federal Aviation Administration's (FAA) Part 21 regulations. Failure to comply can result in fines, legal action, and loss of repeat business.
- Shipping delays - Shipping delays or lost parts that result in downtime can be a significant cost, especially for aviation companies that transport parts internationally.
- Counterfeit parts - Aviation suppliers are seeing an increase in counterfeit parts, which can be difficult to detect and can pose a significant safety risk. An aviation company that inadvertently uses counterfeit parts risks legal action and loss of reputation.
Every industry needs a resilient supply chain
According to Supply Chain Quarterly, a resilient supply chain combines high capacity and a diverse supplier network with highly accurate forecasting, "system thinking," and a culture of continuous improvement.
A decision to reshore inventory and production could be just the motivation you need to fundamentally change your logistics operations to become more resilient and ensure future success.
To determine if you’re ready, ask yourself the following questions and then call us to chat further!
- Are you ready to re-evaluate current inventory management systems to deal with a new set of suppliers?
- Do you need to up your forecasting game to have a clearer understanding of demand patterns and lead time required to fill customer orders?
- Do you have a suitable location in mind where you can rehome employees and find appropriate commercial space for a new warehouse and distribution site?
- Will you be ready to build new relationships and establish clear communication channels to resolve any issues that may arise with new business partners?
About Cura
At Cura Group, we specialize in helping companies build, operate, and manage resilient point-of-use distribution centers to bring essential parts and products close to where they're needed.
Talk to us if you're considering reshoring overseas inventory, or just looking for a smarter way to manage your domestic warehousing and distribution facilities here at home.
Related Blog Posts: